QuickBooks Enterprise has a number of features that help you streamline inventory management, including barcode scanning, multi-location tracking, and serialized inventory tracking.
Wondering if this version of QuickBooks Desktop is right for managing your inventory?
To help you answer this question, we’ll discuss the key inventory management features of QuickBooks Enterprise and provide sample scenarios where you can use these features.
Multiple Warehouse Locations
Enterprise allows you to track inventory across multiple warehouse locations, which can help you optimize inventory levels and reduce shipping times. When you enter a sales or purchase transaction, you can specify which location the inventory is coming from or going to. QuickBooks Enterprise will automatically adjust the inventory levels in each location and update the value of your inventory based on the average cost of the items.
You can also run reports to see the quantity and value of your inventory in each location, as well as view a summary of your inventory levels across all locations. This information can help you make informed decisions about your inventory management and improve your overall business operations.
Sample: A manufacturing company can track inventory levels across multiple production facilities and warehouses to ensure they have the right amount of raw materials and finished products at each location.
Tip: You need to upgrade to Platinum or Diamond to use Advanced Inventory in QuickBooks Enterprise, and in both of these two versions, the Advanced Inventory feature must be enabled first. To do this, you must navigate to Company Preferences under the File menu and location the Advanced Inventory Settings tab.
If you would like to try the full version of QuickBooks Enterprise Desktop, click here to get a free, 30-day no-commitment trial plus access to the Resource Guide that lists all the features available in Enterprise.
Barcode Scanning
Manually entering SKUs can be a time-consuming and error-prone job. That is why barcode scanning in Enterprise is a popular feature for inventory management. Enterprise allows you to use barcode scanning to quickly and accurately track inventory levels, reduce data entry errors, and speed up inventory counts.
Once you have set up your inventory items, you can start scanning them. You can scan items when you receive them, when you pick them up for orders, and when you ship them to customers. The barcode scanner will read the barcode and automatically update the inventory levels in QuickBooks Enterprise.
Sample: A retail store can use barcode scanning to process sales quickly and update inventory levels in real time.
Learn how to set up and use barcode scanning in QuickBooks Enterprise.
Inventory Alerts
Enterprise can send you alerts when inventory levels fall below a certain threshold, helping you avoid stockouts and optimize your inventory levels. You can choose to receive inventory alerts via email, on-screen notifications, or both. This lets you stay informed about your inventory levels, even when you’re not logged into QuickBooks Enterprise.
By using inventory alerts, you can ensure that you always have enough inventory on hand to meet customer demand while minimizing the costs associated with holding excess inventory. This can help you improve your bottom line by reducing the risk of stockouts, lost sales, and overstocking.
Sample: A distributor can set up alerts to notify them when they are running low on a particular product, so they can reorder before running out of stock.
Serialized Inventory Tracking
With Enterprise, you can track inventory by serial number, which can help you keep track of individual items and improve accuracy in warranty claims or product recalls.This feature is particularly useful for businesses that sell high-value items, such as electronics or machinery, and need to keep track of each unit’s movement.
As you buy, sell, or transfer inventory items with serialized tracking, QuickBooks Enterprise will automatically update the inventory records to reflect the movement of each individual unit. You can also generate reports that show the current status of your serialized inventory, such as how many units are in stock, how many have been sold, and to whom.
You can make serial or lot tracking numbers mandatory for sales receipts, item receipts, invoices, adjust quantity, and transfer inventory.
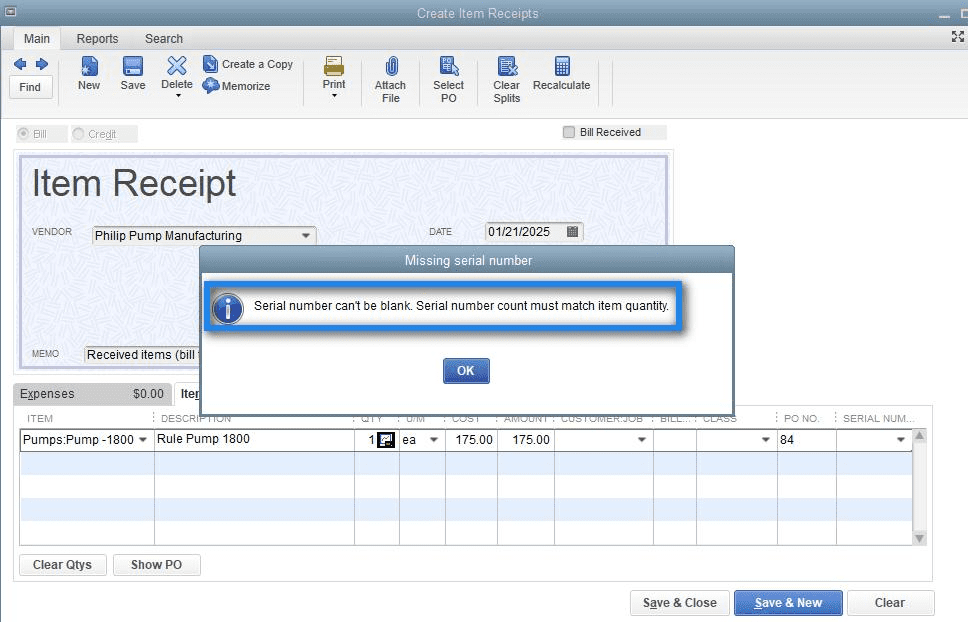
Using serial number to track inventory in QuickBooks
Sample: An electronics manufacturer can track each individual product by its serial number to ensure it meets quality control standards and provide detailed information to customers in case of warranty claims.
Lot Tracking
The program allows you to track inventory by lot number, which can help you manage expiration dates, batch numbers, and product recalls. A lot number is a unique identifier assigned to a group of products that were manufactured or received at the same time and have the same characteristics. This feature helps to ensure accurate inventory counts and reduces the risk of stockouts or overstocks.
Sample: A pharmaceutical company can use lot tracking to ensure they are using the right ingredients in their products, tracking their expiration dates, and tracking which batches of products are affected by recalls.
FIFO Inventory Management
Enterprise offers first-in, first-out (FIFO) inventory management, which helps you ensure that older inventory is sold first to avoid spoilage and obsolescence. This feature is particularly useful for businesses that deal with perishable goods or items with an expiration date, such as food or pharmaceuticals.
Sample: A food retailer can use FIFO inventory management to sell older products first to ensure freshness and minimize waste.
Assembly Builds
Manufacturing firms can use Enterprise to create assembly builds, which can help you track the cost of assembling finished products from raw materials. Assembly builds in Enterprise are used to track and manage the creation of finished products from component parts or raw materials.
When you create an assembly build in QuickBooks Enterprise, you start by creating a new assembly item. This item represents the finished product you want to create. You then add the component parts or raw materials that are needed to build the finished product. These items can either be inventory items or non-inventory items.
Sample: A toy manufacturer can use assembly builds to track the cost of assembling a toy, including the cost of raw materials, labor, and overhead expenses.
Want to learn more about how to use QuickBooks Enterprise? Explore the top 5 inventory management issues you can solve using Enterprise.
Not using QuickBooks Enterprise? Try it for 30 days FREE!
Just register for the free trial below and we will send you everything you need to evaluate QuickBooks Enterprise including 30-day access, sample company files, and the full 88-page QuickBooks Enterprise Guide that details everything that you can do in the software. Free end-to-end consultation and support are included so if you need any help along the way, just let us know!